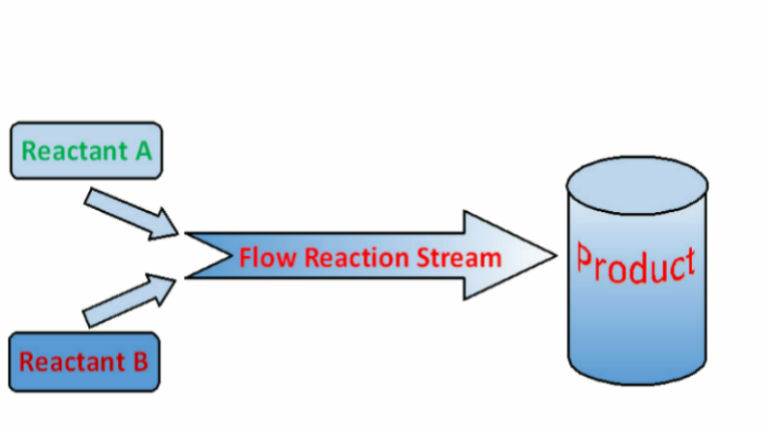
Batch and Flow Chemistry
Chemical reactions generally involve the mixing together of reactive species and the collection of the resulting material which may or may not require purification and analysis.
Batch Chemistry Process
- Reactants are added to a reaction vessel – a test tube, flask or jacketed reactor.
- Mixing takes place and product is generated.
- The process is then stopped and transferred to the next reaction vessel in the sequence or the
product is collected. - Product is generated batchwise.
Flow Chemistry Process
- Reactants are pumped into a tube where the reaction takes place in a stream.
- The product then passes on to the next step in the process or out of the system for use or purification.
- Production is continuous.
Flow Chemistry
- Reactions tend to be highly reproducible, faster with higher yields.
- Excellent temperature control is possible through high surface areas and short residence times.
- Rapid diffusion mixing means that localised hot spots are avoided, resulting in better yields and higher purity, leading to easier work-up. - saving time and materials.
- Flow Chemistry is highly controllable, far higher than in batch operations, opening the way to automation.
- Controllability makes it possible to combine steps sequentially with the product output remaining continuous.
- Low residence times and controllability means that hazardous intermediates formed in-situ and used in the process would be of a small amount and swiftly consumed and flushed away.
Not possible in batch systems. - Scale-up is easier in Flow Chemistry than batch.
- Simply run for longer
- Have a parallel stream
- Move to higher flow rates and larger reactors and continually produce kilogram to multi-kilograms of product.
- Appropriate for a Quality by Design (QbD) approach, resulting in robust and well-understood processes.
Of great importance when scale-up or method transfer is to be considered.
- Flow Chemistry is highly suited to a manufacturing environment where scales can be from laboratory to pilot to process meaning output can be continuous from kg to multiple kgs of product on a daily basis.

Operating Parameters
- Temperature.
- High reactor surface area allows temperature to be raised or lowered very quickly.
- High temperature (>400°C)
- Mixing is less critical due to fast diffusion.
- Residence Time. This is the time the reactants spend in the reaction vessel. – controlled by reactor size and flow rate.
- Reactants
- Reactants may be combined.
- Each reactant may be fed at different rates and points in the flow stream.
- Reactants may be at the same or different molarity.
- Operation with: gases; liquids; and solids. Includes solid phase synthesis.
- Solids can be placed as a packed column or slurry.
- Solvent may be added as a means of separating different processes.
- Pressure control allows heating of volatile solvents beyond their boiling points safely.
- Operations are possible at > 100 Bar.
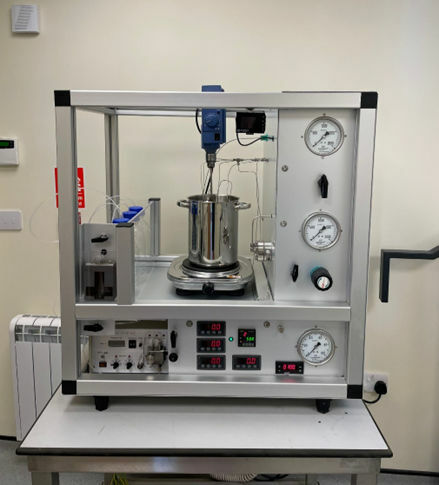
Development System
- Manual parameter setup
- Maximum pressure 100bar.
- Maximum temperature 250°C
- Maximum flow rate 10ml/min
- Automated sampling
- Focus on flexibility and reaction understanding.
- Designed for location in a standard fume hood.
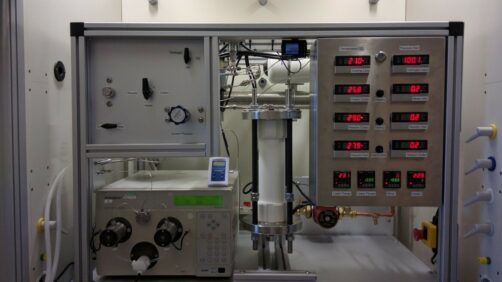
Pilot System
- Manual demonstrator
- Maximum pressure 200bar
- Maximum liquid flow rate 200ml/min
- Maximum temperature 200°C and higher
- Reaction Volume 250ml
- Precise parameter control
- Approximately 1/10 required scale.
- Hydrogen delivery system sized for project.
- Can be designed for location in a standard fume hood.
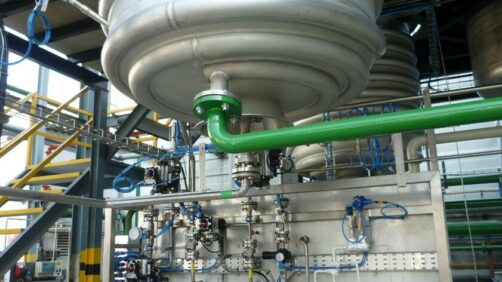
Production System
- Data and experience from running the Development and Pilot systems are used as a base for the design of a production scale system, taking into account the requirements of the customer.